在化工 , 特别是精细化工生产中, 搅拌设备的应用是非常广泛的。搅拌器选用是否合理 , 将直接影响到化学反应的转化率、 收率、 能耗等 , 因此合理的选用搅拌器在工程设计中是不可忽视的。
1 目的和机理
要合理的选用搅拌器 , shou先要了解搅拌目的和搅拌的混合机理。在化工生产中 , 经常有以下几种情况要进行搅拌。
1.1 均相液体混合
把互溶液体混合。通过搅拌尽可能达到分子规模均匀程度。如混酸配制、 石油产品混合等。
1.2 非均相液体混合
把互不相溶的两种液体混合起来, 使其中的一相以微小液滴状均匀分散到另一相液体中去。比如在精细化工制药和食品工业中常会碰到乳化过程, 通过搅拌 , 使**液相以极小的液滴形式分散于第二液相 , 形成稳定的混合物。又如溶剂萃取过程中 , 为了增大液液两相间的界面, 实现相间传质 , 可通过搅拌来完成。
1.3 固液混合
让固体颗粒在液体中悬浮。如在以固体作为催化剂的液相反应中 , 用搅拌器可以防止固体沉降, 提供反应所需的固液传质环境。
1.4 气液混合
在氧化、 加氢和生物发酵等工业操作中 , 搅拌时, 把大气泡打碎成微小气泡并使之均匀分散
到整个液相中 , 以增大气液接触面。
1.5 强化液体与器壁的传热
为了强化流体与器壁之间的传热 , 在器壁处的流体应有足够的流速 , 使介质和器壁面有一个较大的传热系数, 通过搅拌可达此目的。
以上几种情况是化工生产中常见的。在实际的搅拌操作过程中, 常常同时要达到好几种目的。搅拌之所以能达到以上几种目的是因为物料在搅拌作用下相互掺合 , 形成具有某种均匀程度混合的缘故。搅拌器旋转, 推动液体高速流动,同时又带动周围液体, 使全部液体在釜内循环流动, 形成宏观上的总体流动。搅拌器有两大功能:①使液体产生强大的总体流动, 以保证装置内不存在静止区, 达到宏观均匀 ;②产生强大的湍动 , 使液体微团尺寸减小。湍流的强弱在搅拌器的选用过程中是较为重要的一个环节。因为总体流动中高速旋转的旋涡与液体微团之间会产生很大的相对运动和剪切力, 搅拌器选用得当, 搅拌效果越好时 , 液团分割得就越细小 , 使得混合的组分之间接触面不断增大 , 分子扩散速率增加, 混合物的分离强度下降, 也即混合效果越好。
2 分类
化工生产过程中, 通常用到的搅拌器种类有桨式搅拌器、 涡轮式搅拌器、 推进式搅拌器、 锚式搅拌器、 框式搅拌器、 螺带式搅拌器等。各类搅拌器由于其构造 , 性能等差异 , 使其能够分别适用于化工生产中各种不同的工况。以下就各种类型的搅拌器作一简单介绍。
2.1 桨式
桨式搅拌器如图 1 所示。
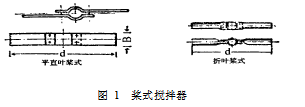
桨式搅拌器又可分为平直叶和折叶搅拌器两种。这类搅拌器的结构和加工都比较简单。搅拌器直径d 与釜径 D 之比 d/D 为 0.35 ~ 0.8 , 其运转速度为 10 ~ 100r/min , 为大型低速搅拌器 , 适用于低、 中等粘度物料的混合及促进传热 , 可溶固体的混合与溶解等场合。运转时以剪切力为主。就平直叶和折叶两种相比较而言, 由于折叶桨式搅拌器的叶片与旋转平面形成夹角 , 因此在旋转时产生的轴向流要大于平直式 , 其宏观混合效果更好些。在实际生产中, 会遇到釜深液高的情况, 此时单层桨式搅拌器难以搅拌均匀, 通常采用的方法是装几层桨叶, 相邻二层桨叶间成90°角交错安装 。由于桨式搅拌器制造和更换方便, 因此常用于化工生产中有防腐蚀和金属污染要求的工况。
2.2 涡轮式
涡轮式搅拌器如图 2 所示。
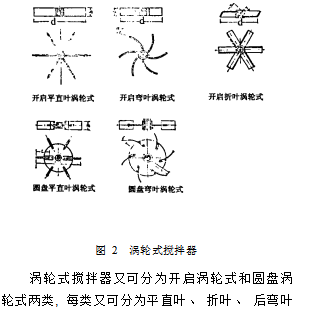
比 d/D 为 0.17 ~ 0.5 , 转速为30 ~ 500r/min 。旋
转时有较高的局部剪切作用 , 能得到高分散度微团, 适用于气液混合及液液混合或强烈搅拌的场合, 常用于低中等粘度物料 (μ<5 ×10
4cP)。就开启式和圆盘式相比较而言 , 其构造上差异造成开启式比圆盘式循环流量更大, 轴向混合效果更好。涡轮式搅拌器的叶片形状除了有平直叶和折叶外 , 还有一种弯叶, 在搅拌中 , 此种叶片受损程度、 消耗功率都低, 适用于固体悬浮、 固体溶解等搅拌场合。
2.3 推进式
推进式搅拌器如图 3 所示。
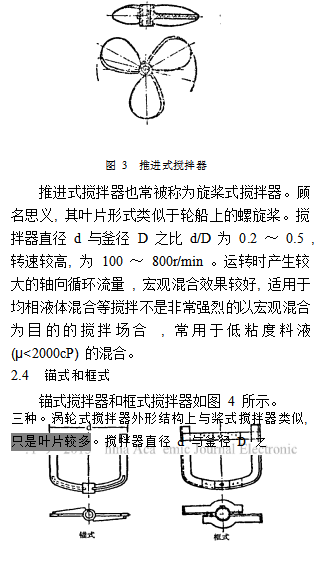
图 4 锚式和框式搅拌器
锚式搅拌器从外形结构上看 , 即在平直叶桨式搅拌器的叶片上加垂直桨叶。而框式搅拌器则在锚式搅拌器上加一横梁。此类搅拌器的一个特点是搅拌外缘与釜壁间隙很小 , d/D 为 0.9 ~ 0.98 , 此特点使得搅拌时物料不易产生死区 。转速为 1 ~ 100r/min , 为低速搅拌器, 只产生切线流, 剪切作用小 , 无轴向混合 , 适用于高粘度(μ<10
5cP)物料的搅拌 。如精细化工产品涂料 、油漆、 化妆品的生产过程中常用到此类搅拌器。
2.5 螺带式
螺带式搅拌器如图 5 所示。
此类搅拌器是把一定螺距的螺旋形钢带固定在搅拌轴上 , 螺带外缘很接近釜壁。搅拌时 , 物料沿釜壁上升, 沿轴向下运动。适用于高粘度料液 (μ<10
5cP)的混合。
3 提高搅拌效率的措施
为了提高搅拌效率, 常采用以下措施。
3.1 挡板
搅拌釜内加挡板有安装竖挡板和横挡板两种。**常用的是沿容器壁垂直安装条形钢板 , 数量一般为 4 块, 宽度为容器直径的 1/12 ~ 1/10 。当容器内径很大和很小时 , 可按实际情况确定挡板数目。安装挡板后 , 作圆周运动的料液遇挡板后, 运动方向发生变化, 在挡板后造成旋涡 , 使切向流改为轴向和径向流 , 而对料液本身的径向流和轴向流没有影响 , 提高了混合效果 , 液面下凹现象消失。
当雷诺数较小时就不应采用挡板, 因为会在档板后面形成停滞区而降低搅拌效果。只有当雷诺数大于 300 时 , 设置挡板才有效。
3.2 导流筒
导流筒限制了循环路径, 减少短路 , 使设备内的物料通过导流筒内的剧烈搅拌以达到预期的搅拌效果。
3.3 非对称性循环回路破坏循环回路的对称性即破坏料液的圆周运动, 消除液面下凹现象。在工程设计中, 常会看到将搅拌器偏心安装或偏心倾斜安装。此种方法常用于小型设备。对于大型容器可将搅拌器偏心水平安装。
4 选用
在搅拌器的选用时 , 可按需搅拌的料液粘度及搅拌目的来选型。
4.1 料液粘度
就搅拌料液的物性来看 , 粘度对搅拌效果的好坏是一个很重要的因素。
低粘度料液混合时的流动形式是湍流 , 运动时高速旋转的旋涡尺寸越小 , 对液体微团的破碎作用越大 , 混合效果就越好。由此看来应选用直径小 , 高转速搅拌器。性能优劣依次为:推进式>涡轮式 >桨式。
反之 , 高粘度料液混合时的流动形式通常是层流。由于料液高粘度这一特性 , 使得搅拌时不能象低粘度料液那样依靠惯性力 , 因此搅拌叶轮直径 d 与釜径 D 之比 d/D 尽量大 , 所以应先选择锚式和框式搅拌器, 也可选螺带式。
4.2 搅拌目的
4.2.1 均相液体混合
均相低粘度液体混合流动状态为湍流 , 即循环流量起决定性因素。按此特点选择的搅拌器依次为 :推进式 >涡轮式 >桨式。
4.2.2 非均相液体混合
为了使其中一相以尽可能小的液滴状均匀分散到另一相中去, 就要求液体被搅拌时有较大的剪切力和循环流量 , 以此来选择的优劣依次为:涡轮式>推进式>桨式。
4.2.3 固液混合
固液混合要求让固体悬浮于液体中需要容积循环好。如固体比重与液体比重差小时, 可选用推进式搅拌器。因为此类搅拌器为轴流型 , 循环速率高。当固体比重与液体比重差大时, 则应选用开启式涡轮搅拌器, 此类搅拌器工作时会把沉降的固体颗粒浮起来而推进式则正好相反。
4.2.4 气液混合
与液液互不相溶混合相似, 在剪切力作用下尽可能将大气泡打碎成小气泡以增大接触面积,
使之均匀分散**液相 , 剪切力起决定作用, 应优 |
先选用涡轮式搅拌器 , 又以平直叶圆盘涡轮搅拌 |
器**为合适。因为此搅拌器中间的圆盘可将气泡 |
(一般由容器底部通入)压**其下, 而后均匀分 |
散**液相 , |
避免了气泡直接由搅拌轴短路。 |
4.2.5 强化液体与器壁的传热 |
此类操作的总体循环流量和换热面积上的高 |
速流动起主要作用, 可优先选用涡轮式搅拌器。 |
5 实例
通过以上分析不难看出, 化工工艺设计中在选用搅拌器时, shou先要分析搅拌的目的 , 再结合所需搅拌的物料的物性综合考虑, 按各类搅拌器的特性进行选用。笔者曾经在某一精细化工项目中遇到一硝化反应过程, 反应是将甲苯以油珠状态分散到混酸中进行硝化。从搅拌目的来看 , 此反应属于互不相溶的液液混合。前面分析过 , 要使互不相溶的液液混合反应充分, 就要使被分散物料甲苯的尺寸越小越好 , 以增加与混酸的接触面积, 这就要求所选用的搅拌器有较好的剪切作用和循环流量, 而涡轮式搅拌器正好符合这一要
求 , 选用后反应效果很好 。
以上所述是理论上及经验上选用搅拌器的方
法和步骤。事实上, 搅拌是一个十分复杂的过程, 搅拌效果和搅拌形式、 尺寸之间很难建立定量关系 , 在实际选用过程中必须通过实验确定 , 通过小试、 中试**后适用于实际生产中 , 即所谓的搅拌器的放大。
化工工艺中经常会遇到一些特殊工况, 按照上述的方法选择单一形式的搅拌器效果不好 , 这就需要通过试验 , 选用不同种类搅拌器进行组合。某个西药的生产过程中有一步氯化反应 :将盐酸加入粉状的环氧物内进行氯化。此反应中没
有加入溶剂溶解粉状物, 所以反应料液状态复 |
杂, 既有粘稠物, 又有粉状物。先采用较常选用 |
的锚式搅拌器进行搅拌 , 但发现反应不充分, 转 |
化率低。分析后发现锚式搅拌器只有在同高度上 |
的环向流而无轴向流, 底部有很多环氧物没有与 |
盐酸反应 , 形成 “死区” 。后来用锚式搅拌器上 |
组装推进式搅拌器 , 以增加轴向流, 结果效果十 |
分明显, 反应转化率迅速提高, 达到了要求。 |
6 结语
综上所述 , 通过对搅拌目的 , 搅拌机理及搅拌器的类型进行分析后 , 不难看出, 化工工艺应按以下方式选用搅拌器。
(1)分析工艺设计中的搅拌目的 :是均相液体混合还是互不相溶的液液混合 ;是固液混合还是气液混合。
(2)结合所需搅拌的物料性质综合考虑, 按各类搅拌器的特性进行选用。
(3)遇到特殊工况时, 还需分析研究 , 在掌握搅拌器的经验用法的同时 , 通过小试、 中试,对搅拌器进行合理选用 , 以达到工艺要求。