1 前 言
气液搅拌反应器广泛应用在石油、化工、生物、制药、食品等行业中。 比如在发酵过程中 ,搅拌的shou要作用是要分散气体 ,增加气液接触面积 ,提高气液传质速率。 针对适用于气液两相搅拌器的研究开发经历了一个漫长的过程 ,这主要是由于气液两相流动状态的复杂性所决定的。相比较而言 ,适用于气液两相搅拌器的研究要落后于单相流搅拌器的研究。近年来 ,随着实验测量技术及计算流体力学技术的发展 ,对气液两相流动行为的研究不断深入 ,各混合设备公司及研究机构也加强了气液两相搅拌器的研究开发力度 ,出现了各种各样的新型气液两相搅拌器。 本文将对气液两相搅拌器的研究历史与现状作简单综述。
2 Rushton 涡轮搅拌器
从 50年代开始 , Rushton涡轮一直被看作是气-
液混合装置的标准配置。 Rushto n涡轮搅拌器的结构比较简单 ,通常是一个圆盘上面带有六个直叶叶片 ,也称为六直叶圆盘涡轮。 由于 Rushton涡轮在许多条件下能够满足工艺的需要 ,同时其结构非常简单 ,容易加工制造 ,所以其应用还是比较广泛的。 但是事实证明:这种结构并不是适用于气液分散的**优结构。 V an 't Riet, Smith 等
[1, 2 ]发现 ,当用六直叶圆盘涡轮式搅拌器把气体分散于低粘流体时 ,在每片桨叶的背面都有一对高速转动的漩涡 ,漩涡内负压较大 ,从叶片下部供给的气体立即被卷入漩涡 ,形成气体充填的空穴 ,称为气穴。 气穴的存在使得搅拌器在充气时的旋转阻力减小 ,因而造成搅拌功率降低。功率的变化使得在装置设计上出现一些问题 ,如果按不充气的功率设计 ,会造成
资源浪费的问题; 如果按充气时的功率设计 ,一旦停止通气 ,功率会迅速上升 ,容易烧毁电机。 气穴的存在还会影响到搅拌槽内的气液传质能力。因为 ,气体并不是直接被搅拌器剪碎而得到分散的。 气泡的分散shou先是在桨叶的背面形成较为稳定的气穴 ,而后气穴在尾部破裂 ,这些小气泡在离心力作用下被甩出 ,并随液体的流动分散**槽内其它区域。
3 弯曲对称叶片搅拌器
气穴理论所揭示的气液分散机理对开发新型搅拌
器有重大意义。 气穴使得 Rush to n涡轮的泵送能力降低。 在高气速下 ,有时整个搅拌器被气穴包围 ,搅拌器近似空转 ,效率很低。 为了改进 Rush to n涡轮搅拌器的缺点 , Smith等提出采用弯曲叶片的概念 ,并解释了弯曲叶片相对于直叶叶片所具有的优点。 弯曲叶片可使其背面的漩涡减小 ,抑制叶片后方气穴的形成。这种结构使该搅拌器具有如下优点: 载气能力提高; 改善了分散和传质能力; 由于通气而造成的搅拌功率下降的程度减小。根据这些研究成果 ,各混合设备公司推出了采用弯曲叶片的搅拌器 , 其中有: Chemineer 公司的
CD-6,如图 2所示; Lightnin公司的 R130搅拌器。 此
类搅拌器的叶片采用的是半管的结构。在湍流条件下 ,
其功率准数一般在 2. 8~ 3. 2之间 , 比 Rushton 涡轮要小得多。后来 ,瑞典 Scaba 公司及英G ICI公司将半管的结构作了进一步改进 ,推出了两种**搅拌器 ,如图 3,图 4所示 ,叶片采取了深度凹陷的结构。
4 弯曲非对称叶片搅拌器
在不充气状况下 ,对各种圆盘涡轮搅拌器来说 ,其流动一般呈对称结构。但在充气条件下 ,由于气体的介
入 ,流动一般说来是非对称的。 因此 ,在设计气体分散搅拌器时 ,将叶片设计成相对于圆盘成对称结构 ,并不是**优化设计。 1998年 , Bakker提出了采用弯曲非对称叶片的想法 ,并据此开发了**新一代的气液混合搅
拌器 BT -6 ( Bakker Turbine ) , 并申请了**
( U SP5791780)。
BT-6搅拌器的特点是采用了上下不对称的结构设计 ,上面的叶片略长于下部的叶片。 该设计使得上升的气体被上面的长叶片盖住 ,避免了气体过早地从叶轮区域直接上升而逃逸 ,而是使更多的气体通过叶轮区域在径向被分散。 该设计既保留了弯曲叶片的优点 ,能减少叶片后方发生气穴 ,同时又能提高气体分散的效率 ,其性能均优于前述的各种径向流气液分散搅拌器。
图
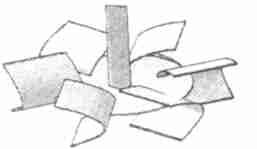
6是在不充气状态
时 Rush ton 涡轮 ( D-6) , CD-6, BT -6搅拌器的搅拌
功率曲线。 从图中可以看
出 , 在湍流区域 , 对 Rush- |
|
ton涡轮其功率准数为 4. |
6 |
图 5 BT -6搅拌器 |
~ 5. |
2,对于 CD-6约为 2. |
8 |
|
~ 3. |
2,而对于 BT -6仅约为 2. |
3。 B T-6的设计更趋合 |
理 ,因而其功率**小。
图 7是在充气状态时三种搅拌器的功率变化曲
线。 从图中可以看出 , Rush to n涡轮功率下降非常明显 ,仅为不充气时的 25% 。 对于 CD-6,充气后功率降为原来的约 70% 。 BT -6在充气后功率变化较小 ,为不充气时的 80% ~ 85% 。
良好的结构设计不仅能够提高气体处理量 ,而且能够提高气液间的传质速率。 实验结果表明 , CD-6的气液间的传质系数较 Rushton 涡轮提高了 40% , 而BT-6 的气液间传质系数较 Rushton 涡轮提高了 60% ,传质效果明显加强。
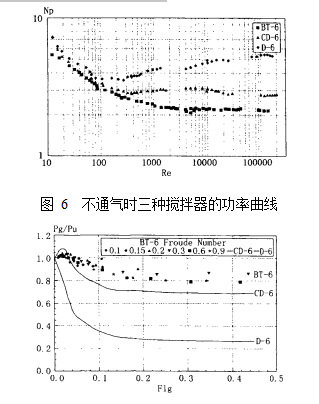
图 7 通气时三种搅拌器的功率曲线
5 轴流式搅拌器
近年来 ,气液分散搅拌器的另一个发展趋势是轴流式搅拌器的设计开发。轴流式搅拌器的特点主要有:能耗低 ,循环量大 ,剪切性能温和等。在许多装置 ,尤其是生化反应器方面应用得越来越广泛。 G内外轴流式搅拌器的应用已经很多
[3 ] ,较典型的有 Pro Chem 公司的 Max flo。 在 800 L罐曲霉的培养下 ,使用该轴流桨比传统的 Rush to n涡轮传质系数提高 40% ,功耗降低
50% 。 还有美G Lightnin公司的 A315搅拌器。 A315
特别适合于气液传质过程 ,在直径大于 1 m 的实验装置中 ,同样的输入功率下 , A315桨的持气量比 Rush-ton涡轮高 80% ,气体分散量提高 4倍 ,同时产量提高
10% ~ 50% ,其剪切力仅为 Rushto n涡轮的 25% , 较
适合于对剪切敏感的过程 ,如微生物的发酵过程等。此
外 ,还有德G Ekato 公司的 InterMig ,法G Ro bin公司的 HPM 等。 此类搅拌器的直径均较传统的 Rushto n 涡轮要大 ,约为槽内径的 47% ~ 60% 。
G内在轴流式搅拌器的研究开发方面已取得许多进展。 北京化工大学开发了 CBY系列搅拌器 ,并对各种工况下的流动场、功耗、以及搅拌器的受力等进行了
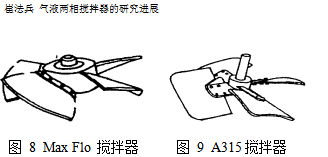
系统的研究 ,而且已经将其成功的推广应用 ,取得了较好的经济效益。华东理工大学开发了翼形桨 ,并提出采用组合桨
[4, 5 ]。 如在青霉素发酵中采用下为 Rushto n 涡轮 ,上为翼形桨的组合。用这种组合代替多层涡轮桨可使主体混合速率提高约 40% 。无锡轻工大学开发了适用于中低粘物系的 LA搅拌器和适用高粘物系的 M T 搅拌器
[ 6]。江苏石油化工学院开发了 JH轴流式搅
拌器
[7 ]。
6 结语及展望
近年来 ,随着先进测试技术 (如 PIV , LDV 等 )及计算流体力学的发展 ,对气液两相体系流动场的研究越来越多 ,而且越来越深入。 如 Friberg
[8 ]将 Mo rud
[9 ] 的计算从二维扩展到三维 ,在三个方向均得到了较好的计算结果 ,而且在计算中还捕捉到了位于叶轮后方的气穴。**近 , Wu
[ 10]将 Rev stedt
[11 ]的大涡模拟方法扩展到了两相流动 ,采用欧拉 -拉各朗日法计算了双层涡轮桨搅拌槽内的气 -液两相流动。其计算结果虽然没有与实验数据进行定量比较 ,但这种方法却是令人鼓舞的。有理由相信 ,将来会有更多高性能的气液搅拌器被开发出来 ,并被推广应用。